RMA QUALITY STANDARD
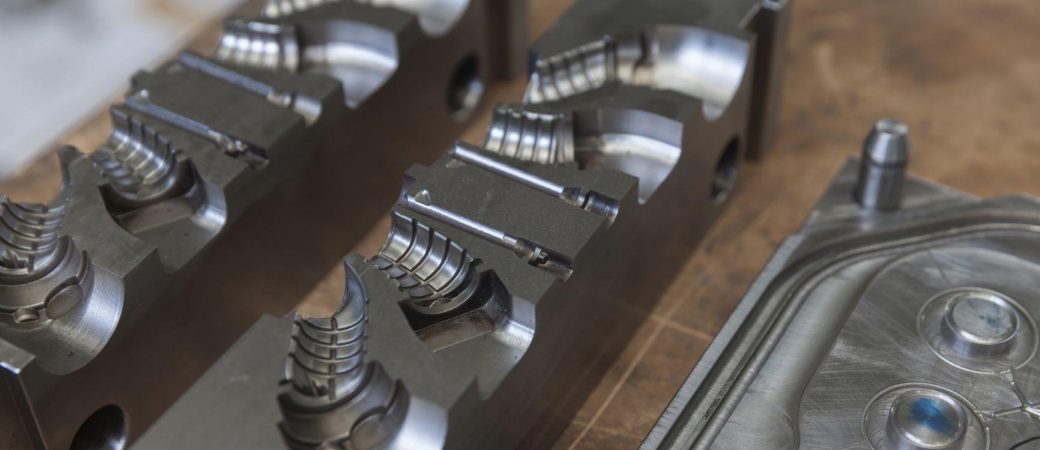
RMA MO-1 Classes and Tolerances for Products Molded in Solid Rubber
RMA MO-1 provides the necessary information to designate a dimensional tolerances, finish tolerances, and flash tolerances for molded rubber parts. The RMA designation is specified as follows:
|
Specification
|
RMA simply refers to the RMA MO-1 specification as the controlling document for the tolerance designation.
Class
|
Classes determine the fixed and closure dimensional tolerances for products molded in solid rubber. The table below shows the 4 classes that are used by RMA.
Class |
Name | Definition |
A1 |
High Precision | This is the tightest tolerance classification and indicates a high precision rubber product. Such moldings require precision molds, fewer cavities per mold, close mix controls, etc., which results in high cost. Optical comparators or other measuring devices may be required to minimize distortion of the rubber part by the measuring instrument. This part requires expensive control and inspection procedures. |
A2 |
Precision | These moldings involve much of the close controls required for the above class. Molds must be precision machined and kept in good repair. While measurement methods may be simpler than the above class, careful inspection will usually be required. |
A3 |
Commercial | This class indicates a general grade or commercial product. This is the most commonly used class. |
A4 |
Non-critical | Molds by this class apply to products were control is non-critical and secondary to cost. |
Based on the class selected, use the corresponding table below to apply tolerances as follows:
- Fixed tolerances are related by size to each dimension but all closure tolerances are determined by the largest closure dimension.
- Tolerances not shown should be determined in consultation with the manufacturer.
- Take special care when applying standard tolerances to products having wide sectional variations.
Metric Tolerances (mm)
Nominal Dimension | A1 | A2 | A3 | A4 | |||||
above | up to and including |
Fixed | Closure | Fixed | Closure | Fixed | Closure | Fixed | Closure |
0 | 10 | 0.1 | 0.13 | 0.16 | 0.2 | 0.2 | 0.32 | 0.32 | 0.8 |
10 | 16 | 0.13 | 0.16 | 0.2 | 0.25 | 0.25 | 0.4 | 0.4 | 0.9 |
16 | 25 | 0.16 | 0.2 | 0.2 | 0.32 | 0.32 | 0.5 | 0.5 | 1 |
25 | 40 | 0.2 | 0.25 | 0.32 | 0.4 | 0.4 | 0.63 | 0.63 | 1.12 |
40 | 63 | 0.25 | 0.32 | 0.4 | 0.5 | 0.5 | 0.8 | 0.8 | 1.25 |
63 | 100 | 0.32 | 0.4 | 0.5 | 0.63 | 0.63 | 1 | 1.1 | 1.4 |
100 | 160 | 0.4 | 0.5 | 0.63 | 0.8 | 0.8 | 1.25 | 1.25 | 1.6 |
160 & over (Multiply by) |
x .004 | x .005 | x .005 | x .008 | x .008 | x .010 |
Inch Tolerances (in)
Nominal Dimension | A1 | A2 | A3 | A4 | |||||
above | up to and including |
Fixed | Closure | Fixed | Closure | Fixed | Closure | Fixed | Closure |
0 | 0.40 | 0.004 | 0.005 | 0.006 | 0.008 | 0.008 | 0.013 | 0.013 | 0.032 |
0.40 | 0.63 | 0.005 | 0.006 | 0.008 | 0.010 | 0.010 | 0.016 | 0.016 | 0.036 |
0.63 | 1.00 | 0.006 | 0.006 | 0.010 | 0.013 | 0.013 | 0.020 | 0.020 | 0.040 |
1.00 | 1.60 | 0.008 | 0.010 | 0.013 | 0.016 | 0.016 | 0.025 | 0.025 | 0.045 |
1.60 | 2.50 | 0.010 | 0.013 | 0.016 | 0.020 | 0.020 | 0.032 | 0.032 | 0.050 |
2.50 | 4.00 | 0.013 | 0.016 | 0.020 | 0.025 | 0.025 | 0.040 | 0.040 | 0.056 |
4.00 | 6.30 | 0.016 | 0.020 | 0.025 | 0.032 | 0.032 | 0.050 | 0.050 | 0.063 |
6.30 & over (Multiply by) |
x .004 | x .005 | x .005 | x .008 | x .008 | x .010 |
Finish
RMA | A2 | – | F3 | – | T.003 |
A finish symbol is comprised of “F” and a number from the following table. Since not all surfaces require the same finish, the drawing should indicate the area for the finish being specified. Use of a “Commercial Finish” (F3) is recommended where possible.
Drawing Designation |
Description |
F1 |
A smooth, polished and uniform finish completely free of tool marks, dents, nicks and scratches, as produced from a highly polished steel mold. In areas where F1 is specified, the mold will be polished to a surface finish of 10 micro-inches (250nm) or better. |
F2 |
A uniform finish as produced from a polished steel mold. In areas where F2 is specified, the mold will be polished to a surface finish of 32 micro-inches (800nm) of better but with very small tools marks not polished out. |
F3 |
Surfaces of the mold will conform to good machine shop practice and no micro-inch finish will be specified. This is “Commercial Finish”. |
F4 |
Satin finish. |
Standards for Finish and Appearance
- Machine Finish of the Mold – The finish of the mold affects the surface finish and appearance of the final molded part. A highly polished steel mold, without defects or tool marks, provides a superior finish. A chrome-plated mold may be required in some cases to meet demanding production requirements. However, the average commercial mold is competently machined and typically displays tool marks. The deciding factor in mold finish is normally cost. Finally, the material being molded and the molding processes used may have greater bearing on the final part than mold finish.
- Type of Material Used – The material chosen for the part is critical to its look and feel. Some materials are inherently glossy or dull, while others may dull over time or with handling. Anti-ozone agents, added to some compounds to protect them from the effects of ozone, may bleed affecting the color, gloss or feel of the surface. Type of material or other design or manufacturing requirements may preclude the molding of a glossy-surfaced part.
- Mold Release Lubricant – Mold release lubricant may leave an oily film on the surface of the part. This may affect appearance or adhesion ability. Some materials release from the mold with little or no lubricant. These factors should be addressed in specification of a part.
- Flash Removal – Method of flash removal may affect the look and feel of the finished part. For example, tumbling may dull the part while hand trimming may barely affect an edge.
Flash
|
Flash Designations
- Extension – Designated by a ‘T’ and the maximum extension in thousandths of an inch or millimeters. For example: T .032 indicates a .032 inch maximum extension and T .80mm indicates an .80mm maximum extension.
- Thickness – May be specified following the extension designation if critical to the part’s function. Closure tolerances from tables apply.
- Location – An arc marking the area and a leader to the trim symbol indicates the flash specifications at this location. If flash is unacceptable at the location, use T .000.
- Standards – The drawing may indicate maximum flash extension permissible, see the table below. Naturally, assigning a trim symbol to an area should be consistent with the function of the product and, for the sake of simplicity, only areas requiring a designation should be specified. A standard note can often be used without additional notation.
Drawing Designation |
Description |
T.000 |
(T.00mm) No flash permitted on area designated. (Standard notation regarding other surfaces must accompany this notation.) |
T.003 |
(T.08mm) This tolerance will normally require buffing, facing, grinding or a similar operation. |
T.016 |
(T.40mm) This tolerance will normally require precision die trimming, buffing or extremely accurate trimming. |
T.032 |
(T.80mm) This tolerance will normally necessitate die trimming, machine trimming tumbling or hand trimming. |
T.063 |
(T1.60mm) This would be the normal tear trim tolerance. |
T.093 |
(T2.35mm) This tolerance will normally require die trim, tear trim, or hand trim of some type. |
T.8 |
(T.8) No flash limitation. |
Flash Terminology
- “Flash” is excess material typically resulting from cavity overflow. It is common to most molding operations.
- “Flash Extension” is the excess material extending from the part along the mold parting line.
- “Flash Thickness” varies due to mold closure tolerances and is measured perpendicular to the parting line.
Design Issues
Manufacturer and designer should discuss flash-related issues in order to avoid errors in mold design and parting line location, optimize cost and production by appropriately finishing parts, offer access to uniform molded products regardless of source and simplify quality inspection. In specific Flash Extension and Flash Thickness tolerances should be clearly communicated. It is not the designer’s responsibility to determine methods of flash removal, only acceptable levels of tolerance and parting line location.
Flash removal is a significant cost factor in the molding process. Hand trimming, tumbling, wire brushing, abrasive removal or spot facing are all options of the manufacturer. It is cost-efficient to accurately specify the widest tolerances with regard to flash thickness, extension and position without affecting the part’s function and appearance. In some cases, flash removal may be unnecessary or even proscribed. In other cases, flash tightly adhered to inserts may be acceptable. In addition, “Flashless” molding, where the parting line is minimized without significant thickness or extension, is achievable at a cost.
Setting Flash Standards
- Parting Line Location – Flash lines must be located to allow part removal from the mold cavity after curing and, if applicable, locations where parting lines are acceptable should be designated.
- Flash thickness depends on mold design and closing pressure, type of material being molded, weight and shape of charge and other factors. Typical variations in flash thickness are indicated in closure tolerance tables. Also, thick flash may be encountered where there are handling issues and thickness has no bearing on function or appearance.
- Flash Extension – Depending on flash location, flash thickness, and other factors, flash extension can be removed to meet a specific extension, zero extension or even a cut back into the part.
Flash Extension Removal
Flash extension may be removed through a variety of techniques including:
- Buffing – A moving abrasive surface is used to remove excess material.
- Die Trim – A hand or machine-mounted shaped cutting tool presses the flash extension against a flat plate or a fitted shape to shear or pinch off excess flash. Machine dies are often used in high-output situations for trimming of uniform parts from multi-cavity molds.
- Machine Trim – The part is passed through rotating or reciprocating cutting tools to shear, saw, or pare flash.
- Tumbling – Tumble trimming features a barrel or drum that rotates allowing the parts to bump together causing the thin, fragile flash to break off. Dry tumbling, effective with harder (higher durometer) materials, is performed at room temperature. Refrigerant-based tumbling, freezing the parts with a refrigerant such as carbon dioxide, makes the part brittle and facilitates flash break away. In both cases, tumbling affects the finish and appearance of the part.
- Mechanical Deflashing – Flash is removed in specially designed machinery using an abrasive, a freezing agent and a tumbling chamber under careful timing and supervision. The process is designed to freeze and abrade the flash before the body of the part has lost any elasticity. Of course, surface finish may be affected and abrasive medium may need to be cleaned off the finished parts.
- Pull or Tear Trim – The flash extension closest to the part is purposefully molded very thin allowing it to pull away at that (thinnest) point. Since this may result in a less than perfect edge, this method of flash removal should be limited to non-critical applications.
- Hand Trim – Flash is hand removed by workers using tools like knives, razor blades or scissors.