Norme de qualité de la RMA
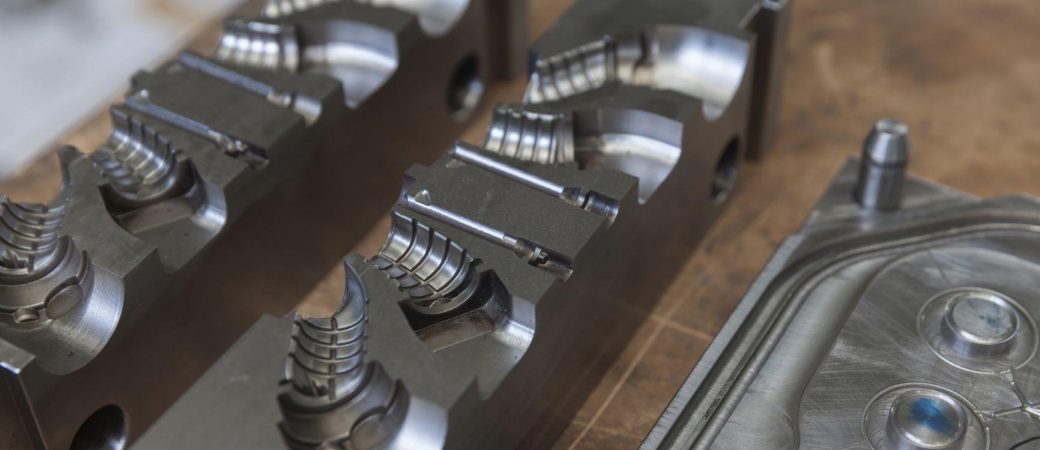
RMA MO-1 : Classes et tolérances pour les produits moulés en caoutchouc solide
La spécification RMA MO-1 fournit l’information nécessaire pour désigner les tolérances dimensionnelles, les tolérances de finition et les tolérances de bavure pour les pièces de caoutchouc moulé. La désignation RMA est spécifiée comme suit :
|
Spécification
|
RMA fait simplement référence à la spécification RMA MO-1 à titre de document de contrôle pour la désignation de tolérance.
Classe
|
Les classes déterminent les tolérances dimensionnelles fixes et de fermetures pour les produits moulés en caoutchouc solide. Le tableau ci-dessous présente les quatre classes utilisées par la RMA.
Classe |
Nom | Définition |
A1 |
Précision élevée | La plus haute classification de tolérance; elle indique un produit de caoutchouc de précision élevée. Ces types de moulages requièrent des moules de précision, une quantité moindre de cavités par moule, une gestion serrée des mélanges, etc., ce qui entraîne des coûts élevés. Il peut s’avérer nécessaire d’avoir recours à des comparateurs optiques ou à d’autres appareils de mesure pour minimiser la distorsion de la pièce moulée par l’instrument de mesure. Cette étape nécessite des procédures coûteuses de contrôle et d’inspection. |
A2 |
Précision | Ces moulages exigent des contrôles serrés, semblables à ceux requis pour la classe précédente. Les moules doivent être usinés avec précision et conservés en bon état. Bien que les méthodes de mesure puissent être plus simples que pour la classe précédente, une inspection méticuleuse est habituellement requise. |
A3 |
Commercial | Cette classe indique une catégorie générale ou un produit commercial. C’est la classe la plus couramment utilisée. |
A4 |
Non essentiel | Les moulages de cette classe font référence à des produits pour lesquels un contrôle n’est pas essentiel et représente un aspect subordonné au coût. |
Selon la classe sélectionnée, utiliser le tableau correspondant ci-dessous pour choisir les tolérances :
- Les tolérances fixes sont reliées par volume à chaque dimension, mais toutes les tolérances de fermetures sont déterminées par la plus grande dimension de fermeture.
- Les tolérances non indiquées doivent être déterminées en consultation avec le fabricant.
- Des précautions doivent être prises dans l’application des tolérances standards pour les produits présentant de fortes variations sectionnelles.
Tolérances métriques (mm)
Dimension nominale | A1 | A2 | A3 | A4 | |||||
Au-dessus de | Jusqu’à et incluant |
Fixe | Fermeture | Fixe | Fermeture | Fixe | Fermeture | Fixe | Fermeture |
0 | 10 | 0.1 | 0.13 | 0.16 | 0.2 | 0.2 | 0.32 | 0.32 | 0.8 |
10 | 16 | 0.13 | 0.16 | 0.2 | 0.25 | 0.25 | 0.4 | 0.4 | 0.9 |
16 | 25 | 0.16 | 0.2 | 0.2 | 0.32 | 0.32 | 0.5 | 0.5 | 1 |
25 | 40 | 0.2 | 0.25 | 0.32 | 0.4 | 0.4 | 0.63 | 0.63 | 1.12 |
40 | 63 | 0.25 | 0.32 | 0.4 | 0.5 | 0.5 | 0.8 | 0.8 | 1.25 |
63 | 100 | 0.32 | 0.4 | 0.5 | 0.63 | 0.63 | 1 | 1.1 | 1.4 |
100 | 160 | 0.4 | 0.5 | 0.63 | 0.8 | 0.8 | 1.25 | 1.25 | 1.6 |
160 & plus (Multiplié par) |
x .004 | x .005 | x .005 | x .008 | x .008 | x .010 |
Tolérances en pouces (po)
Dimension nominale | A1 | A2 | A3 | A4 | |||||
Au-dessus de | Jusqu’à et incluant |
Fixe | Fermeture | Fixe | Fermeture | Fixe | Fermeture | Fixe | Fermeture |
0 | 0.40 | 0.004 | 0.005 | 0.006 | 0.008 | 0.008 | 0.013 | 0.013 | 0.032 |
0.40 | 0.63 | 0.005 | 0.006 | 0.008 | 0.010 | 0.010 | 0.016 | 0.016 | 0.036 |
0.63 | 1.00 | 0.006 | 0.006 | 0.010 | 0.013 | 0.013 | 0.020 | 0.020 | 0.040 |
1.00 | 1.60 | 0.008 | 0.010 | 0.013 | 0.016 | 0.016 | 0.025 | 0.025 | 0.045 |
1.60 | 2.50 | 0.010 | 0.013 | 0.016 | 0.020 | 0.020 | 0.032 | 0.032 | 0.050 |
2.50 | 4.00 | 0.013 | 0.016 | 0.020 | 0.025 | 0.025 | 0.040 | 0.040 | 0.056 |
4.00 | 6.30 | 0.016 | 0.020 | 0.025 | 0.032 | 0.032 | 0.050 | 0.050 | 0.063 |
6.30 & plus (Multiplié par) |
x .004 | x .005 | x .005 | x .008 | x .008 | x .010 |
Fini
|
Un symbole de fini est composé de la lettre « F » et d’un nombre indiqué dans le tableau suivant. Étant donné que toutes les surfaces ne requièrent pas le même fini, le dessin devrait indiquer l’emplacement du fini spécifié. L’utilisation d’un « fini commercial » (F3) est recommandée autant que possible.
Désignation sur dessin |
Description |
F1 |
Un fini lisse, poli et uniforme, ne présentant ni marque d’outils, ni entailles, encoches ou égratignures, tel que produit par un moule en acier à poli élevé. Pour les emplacements identifiés par la désignation F1, les moules seront polis jusqu’à obtention d’un fini de surface de 10 micropouces (250nm) ou mieux. |
F2 |
Un fini uniforme tel que produit par un moule en acier poli. Pour les emplacements identifiés par la désignation F2, le moule sera poli jusqu’à obtention d’un fini de surface de 32 micropouces (800nm) ou mieux, mais comportant de très fines marques d’usinage non effacées par le polissage. |
F3 |
Les surfaces du moule seront le résultat de bonnes pratiques d’usinage et aucun fini en micropouce ne sera spécifié. C’est ce qu’on appelle un « fini commercial ». |
F4 |
Fini satiné. |
Normes pour le fini et l’apparence
- Fini usiné du moule – Le fini du moule a un impact sur le fini de surface et sur l’apparence finale de la pièce moulée. Un moule en acier à poli élevé, sans défauts ou marques d’usinage, offre un fini supérieur. Un moule chromé peut être nécessaire dans certains cas pour se conformer à des paramètres de production exigeants. Cependant, la plupart des moules commerciaux sont usinés correctement et présentent des marques d’usinage. Habituellement, c’est le coût qui constitue le facteur déterminant en matière de fini. Enfin, le matériau moulé et le processus de moulage utilisé peuvent avoir un impact plus important sur la pièce finale que le fini du moule.
- Type de matériau utilisé – Le matériau sélectionné joue un rôle crucial dans l’aspect final et la texture de la pièce. Certains matériaux ont un aspect naturellement mat ou lustré, alors que d’autres peuvent devenir mat avec le temps ou à force d’être manipulés. Certains agents anti-ozone, ajoutés à certains composants pour les protéger des effets de l’ozone, peuvent affecter la couleur, l’aspect lustré ou la texture de la surface. Le type de matériau ou certaines exigences ayant trait au design ou à la fabrication peuvent rendre impossible le moulage d’une pièce à surface lustrée.
- Lubrifiant de démoulage – Le lubrifiant de démoulage peut déposer une pellicule huileuse sur la surface de la pièce. Ceci peut avoir un impact sur l’apparence ou sur la capacité d’adhésion. Certains matériaux sont dégagés du moule avec très peu ou pas du tout de lubrifiant. Ces facteurs devraient être abordés lors de la spécification d’une pièce.
- Ébavurage – La méthode d’ébavurage peut avoir un impact sur l’aspect et la texture de la pièce finie. Par exemple, l’abrasion au tonnelage peut atténuer l’aspect lustré d’une pièce, alors que le taillage à la main peut à peine affecter une arête.
Bavure
|
Désignations en matière de bavure
- Excédent – Désigné par la lettre « T » et par l’excédent maximal en milliers de pouce ou de millimètres. Par exemple : T .032 indique un excédent maximal de .032 po, et T .80mm indique un excédent maximal de .80mm.
- Épaisseur – Peut être spécifiée après la désignation d’excédent si elle est essentielle à la fonction de la pièce. Les tolérances de fermetures indiquées dans les tableaux sont applicables.
- Emplacement – Une indication de détail suivie d’un point de conduite menant au symbole d’ébarbage ‘’T’’ indique le niveau spécifique de bavure à respecter à cet endroit. Si la bavure est inacceptable pour cet emplacement, utiliser T .000.
- Normes – Le dessin peut indiquer l’excédent maximal de bavure autorisé; voir le tableau ci-dessous. Naturellement, l’attribution d’un symbole d’ébavurage à un endroit doit être cohérente avec la fonction du produit et, à des fins de simplicité, seuls les emplacements exigeant une désignation devraient être spécifiés. Une note standard peut souvent être utilisée sans notation additionnelle.
Désignation sur dessin |
Description |
T.000 |
(T.00mm) Aucune bavure autorisée à l’emplacement désigné. (Une notation standard concernant les autres surfaces doit accompagner cette notation.) |
T.003 |
(T.08mm) Cette tolérance exige habituellement un polissage au feutre, un limage, un ponçage ou une autre opération du même type. |
T.016 |
(T.40mm) Cette tolérance exige habituellement une découpe d’ébavurage, un polissage de précision ou un découpage de très haute précision. |
T.032 |
(T.80mm) Cette tolérance exige habituellement une découpe d’ébavurage, un découpage à la machine, un tonnelage ou un découpage à la main. |
T.063 |
(T1.60mm) Indique une tolérance de découpage par déchirure habituelle. |
T.093 |
(T2.35mm) Cette tolérance exige habituellement une découpe d’ébavurage, un découpage par déchirure ou un découpage à la main. |
T.8 |
(T.8) Aucune limite de bavure. |
Terminologie en matière de bavure
- La « bavure » représente le trop-plein de matériau qui s’échappe de la cavité d’un moule pendant le moulage. C’est un aspect courant de la plupart des opérations de moulage.
- « L’excédent de bavure » représente l’excédent de matériau qui se dégage du plan de joint du moule.
- « L’épaisseur de bavure » varie en fonction des tolérances de fermetures de moule et est mesurée perpendiculairement au plan de joint du moule.
Problèmes relativement à la conception
Le fabricant et le concepteur devraient discuter des problèmes reliés aux bavures afin : d’éviter des erreurs dans la conception des moules et de l’emplacement des plans de joint, d’optimiser les coûts et la production en effectuant un finissage approprié, d’offrir un accès à des produits moulés de manière uniforme, peu importe la source, et de simplifier l’inspection de qualité. Les tolérances spécifiques relatives aux excédents de bavure et aux épaisseurs de bavure devraient être communiquées très clairement. Le concepteur n’a pas la responsabilité de déterminer les méthodes d’ébavurage; il doit seulement déterminer les niveaux de tolérance acceptables et l’emplacement des plans de joint.
L’ébavurage constitue un facteur économique significatif dans le processus de moulage. L’ébarbage à la main, le tonnelage, le brossage métallique, l’utilisation de matière abrasive ou le limage constituent tous des options pour le fabricant. Il est rentable de spécifier de manière exacte les tolérances les plus larges relativement à l’épaisseur, à l’excédent et à la position de la bavure, sans affecter la fonction et l’apparence de la pièce. Dans certains cas, l’ébavurage peut être superflu ou même proscrit. Dans d’autres cas, la bavure qui adhère étroitement aux insertions peut être acceptable. De plus, moyennant un certain coût, il est possible d’obtenir un moulage « sans bavure », soit lorsque le plan de joint du moule est minimisé sans produire d’épaisseur ou d’excédent significatifs.
Établir des normes relativement aux bavures
- Emplacement du plan de joint – Les lignes de bavure doivent être identifiées afin de dégager la pièce de la cavité du moule après la cuisson et, dans certains cas, les emplacements de plans de joint acceptables devraient être désignés.
- L’épaisseur de la bavure dépend de la conception du moule et de la pression de fermeture, du type de matériau utilisé pour le moulage, du poids et de la forme de la charge, ainsi que d’autres facteurs. Les variations typiques en matière d’épaisseur de bavure sont indiquées dans les tableaux de tolérances de fermetures. De plus, une bavure d’une certaine épaisseur peut se présenter dans le cas de problèmes de manipulation et lorsque l’épaisseur n’a pas d’impact sur la fonction ou l’apparence.
- Excédent de bavure – Selon l’emplacement de la bavure, de son épaisseur et d’autres facteurs, l’excédent de bavure peut être éliminé afin d’atteindre un excédent spécifié, une absence d’excédent ou même une retaille dans la pièce.
Élimination de l’excédent de bavure
On peut éliminer l’excédent de bavure de diverses manières, incluant les suivantes :
- Polissage – Une surface d’abrasion rotative est utilisée pour retirer l’excédent de matériau.
- Découpe d’ébavurage – Un outil de découpage à la main ou monté sur machine comprime l’excédent de bavure contre une tôle plate ou une forme ajustée pour cisailler ou pincer l’excédent de bavure. On utilise souvent des machines dans des situations de production en grande série pour tailler des pièces uniformes provenant de moules à cavités multiples.
- Ébarbage à la machine – La pièce est introduite dans des outils de découpe rotatifs ou à mouvement alternatif afin de cisailler, de scier ou de réduire la bavure.
- Tonnelage – L’abrasion au tonnelage consiste à utiliser une cuve ou un tambour en rotation, ce qui permet aux pièces d’entrer en contact les unes avec les autres et de casser les bavures minces et fragiles. Le tonnelage à sec, efficace pour les matériaux plus durs (à duromètre plus élevé), est effectué à température de la pièce. Le tonnelage frigorigène, qui consiste à geler les pièces à l’aide d’un réfrigérant tel que le dioxyde de carbone, a un effet cassant sur le matériau et facilite l’élimination de la bavure. Dans les deux cas, le tonnelage a un impact sur la finition et l’apparence de la pièce.
- Ébavurage mécanique – La bavure est retirée à l’aide d’un appareil spécialement conçu et d’un abrasif, d’un agent cryogénique et d’une chambre de tonnelage, sous étroite surveillance et selon une durée déterminée. Le processus est conçu pour geler et éroder la bavure avant que le corps de la pièce ne perde son élasticité. Bien entendu, la finition de surface peut être affectée et il se peut que le média abrasif doive être nettoyé des pièces finies.
- Ébarbage par tirage ou déchirage – L’excédent de bavure positionné le plus près de la pièce est volontairement moulé très mince, ce qui permet de l’extraire en tirant sur le point le plus mince. Étant donné que cette méthode d’élimination de bavure peut produire une arête imparfaite, elle ne devrait être utilisée que pour les utilisations non critiques.
- Ébarbage à la main – La bavure est retirée à la main par des travailleurs à l’aide d’outils tels que des couteaux, des lames de rasoir ou des ciseaux.